The legal constitution of GNOSIS was established through the Consortium
Cooperation Agreement finalized in February 1993. This section summarizes the
objectives, activities and organization of the test case as agreed by the
consortium
The present global manufacturing environment is plagued by several problems:
scarcity of natural resources, environmental destruction, and regional trade
imbalances. The GNOSIS project is founded on the hypothesis that final
resolution of these problems requires a radical departure from the present
manufacturing paradigm. The overall long-term objective of the project is to
realize a new manufacturing paradigm, the "post mass production paradigm", that
can form a basis of manufacturing industrial products in a sustainable way in
the foreseeable future. To reach the overall objective, the project will
conduct research on the enabling methods and technologies required for the new
paradigm, and on development strategies for reaching the new paradigm. These
methods, technologies, and strategies will provide benefits in the
short-to-intermediate term in addition to long-term advances. Figure 2 shows
the critical parameters in developing a post mass production paradigm which
have shaped GNOSIS research activities.
The new paradigm recognizes that all resources are ultimately limited.
Therefore, resource use must be reduced and waste generation eliminated
throughout the entire product life-cycle. The GNOSIS project hypothesizes that
this will require radically new types of products and processes -- soft
products and soft factories. Soft products and soft factories are
reconfigurable systems designed to be robust to failures and changes in their
environment. Their design and production process, from raw materials to
products to reuse or disposal, will support sustainable growth and
environment-consciousness. Low resource use is achieved by multi-functionality,
adaptability, reconfigurability, and reuse.
Soft products and soft factories require communication and knowledge sharing
across the boundaries of individual companies, technical domains, and time. To
realize this, the knowledge must be systematized to ensure that it is generally
available and reusable throughout the life-cycle.
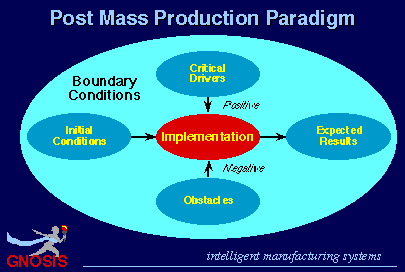
Figure 2 Critical parameters in developing a post mass production
paradigm
In order to progress towards the goals indicated above, work has proceeded
within the following research streams:
Systematization of knowledge and supporting information for design and
manufacturing: Knowledge systematization methods and tools are investigated and
demonstrated to support the activities of the other streams.
Configuration management systems: The focus of the work is the formalization of
manufacturing problems and constraints in a distributed environment based on
the sharing and reuse of product and manufacturing knowledge.
Configurable production systems: Research will investigate configurable
production systems, production control, and factory design principles, with the
longer-term goal of enabling soft factories and reuse of production process
knowledge.
Soft machinery: Research utilizes the results of the other streams to develop
conceptual prototypes of next-generation soft artifacts.
Post mass production paradigm: Research concentrates on the characterization of
the post mass production paradigm and its development strategies.
The relationship between the research streams is shown in Figure 3.
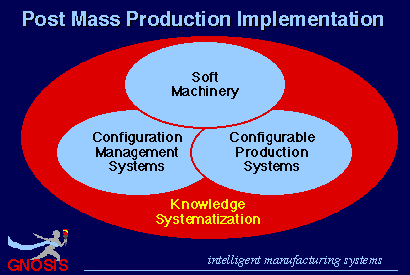
Figure 3 GNOSIS test case relations between work streams
The research has been divided into work packages within which various tasks
have to be carried out, as set out below. MW1 and MW2 are meta-work packages,
DW1 is a definition work package, and TW1 to TW5 are technical work packages.
Each technical work package (TW) involves defining the research topics,
surveying the state of the art, evaluating emerging technologies, carrying out
the research and producing deliverables.
- MW1: Project Coordination
- General project management
- Workshop organization
- MW2: Reporting of Results
- Report to IMS secretariats
- Conclusions from the test case
- Identification of key topics for future IMS program
- International publications
- Report to standardization bodies
- DW1: Definition of Terminology and Demonstration Examples
- Definition of research terminology
- Definition of test case demonstration examples
- TW1: Systematization of Knowledge and Supporting Information for Design
and Manufacturing
- Definition of functional knowledge for design and manufacturing
- Establishment of research environment for knowledge systematization
- TW2: Configuration Management Systems
- Survey of state-of the-art of configuration management systems
- Definition and formalization of configuration problem
- Configuration management software and model development
- TW3: Configurable Production Systems
- Control architecture for configurable production
- Production scheduling based on product knowledge
- Production control using scheduler
- Factory simulator to test control and scheduling systems
- TW4: Soft Machinery
- Product knowledge and intelligence
- Reconfigurable products and machinery
- Autonomous control
- Self-maintaining and autonomous products
- TW5: Post Mass Production Paradigm
- Establishment of a framework for systematization of future scenarios
- Comparison and integration of individual partner views of a post mass
production paradigm
- Embedding the comprehensive view into the GNOSIS scope
The thirty one partners in GNOSIS participated in different combinations of
technical work packages. There was substantial overlap in membership of all
packages as shown in Figure 4 which supported the coordination indicated in
Figure 3. Overall coordination was through 4 inter-regional meetings, and
additional work package coordination through 8 specialist meetings as shown in
Figure 5.
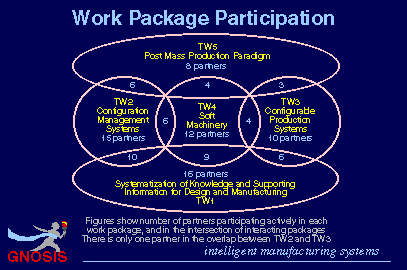
Figure 4 GNOSIS test case technical work package participation
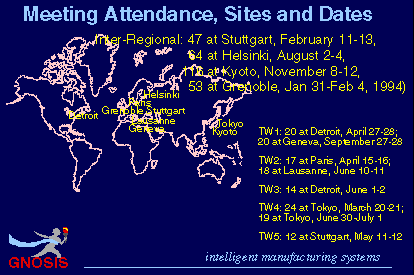
Figure 5 GNOSIS test case major meetings
The main features of the project management structure are as illustrated in
Figure 6. The Technical Work Packages are directly under the Executive
Committee, leading their respective assignments across all regions. This
structure was derived from the original proposed management structure, and was
found to be the most useful for the effective steering of the consortium.
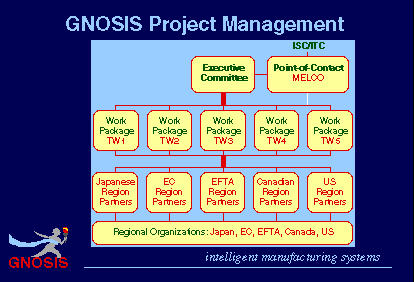
Figure 6 GNOSIS test case project management
- The point-of-contact for the consortium is Mitsubishi Electric.
- A regional project manager has been appointed for each region who is
maintaining close contact with the equivalent project managers in collaborating
groups.
- Each work package has a responsible leader.
- An executive committee has been formed, consisting of the project managers
of coordinating companies and responsible leaders of work packages.
- The executive committee is responsible for disseminating information among
regional partners and for coordinating final decisions regarding the content
and direction of the research.
- Three inter-regional meetings of all partners covering all work packages
have been organized, chaired by the executive committee, in order to review the
deliverables and evaluate the progress of the project.
- A special exchange program whereby researchers from different regions are
being exchanged has been established in order to ensure smooth interaction and
coordination between different work packages.
The research has been
reported through consortium progress reports to ISC and ITC. These reports form
the basis for conference and journal papers which will subsequently be made
public. Appraisals of the mechanism for deploying research results and
prototypes and for technology transfer have taken place at the regular
inter-regional and the executive committee meetings.
The partners involved in GNOSIS are shown below. There have been no changes
during the test case. All 31 of the original partners have been active
participants in the work packages on a continuing basis.
Region Regional Coordinator Partner
Japan Mitsubishi Electric Corp. +Mitsubishi Electric Corp.
Nissan Motors Ltd
Fuji Xerox Ltd
Kajima Corp.
Shimizu Corp.
The University of Tokyo
Tokyo Institute of Technology
Kyushu Institute of Technology
EC ADEPA, France ADEPA Agence de la Productique, France
Télémécanique S.A., France
ARM Conseil, France
IBM, France
ITMI - GROUPE CAP GEMINI SOGETI, France
LLP/CESALP University of Savoie, France
Fraunhofer Institute IPA, Germany
MAN Roland, Germany
Brose, Germany
BICC plc, UK
Cambridge University, UK
EFTA ABB, Finland ABB Corporate Research, Finland
Tehdasmallit Oy, Finland
Synergy Center Ltd, Finland
SIMSON Development Program, Finland
VTT Technical Research Centre of Finland
Tampere University of Technology, Finland
EPFL Swiss Federal Institute of Technology, Switzerland
ETHZ Swiss Federal Institute of Technology, Switzerland
Canada Alberta Research Council Alberta Research Council
Division of Manufacturing Eng., University of Calgary
Knowledge Science Institute, University of Calgary
USA Deneb Robotics Inc Deneb Robotics Inc
+ Mitsubishi Electric Corp. is the International Point of Contact.
Contents,
Previous
Section,
Next
Section,
IMS
Page,
KSI
Page
gaines@cpsc.ucalgary.ca 1-Sep-94